Single pile vertical compression test
The principle of single pile vertical compressive static load test is to apply load step by step on the top of the pile, and observe the settlement of the pile under the load, so as to test the vertical compressive bearing capacity of the single pile. Single pile vertical compression test equipment is mainly composed of reaction force device, loading device, load measuring device, displacement measuring device and automatic acquisition device.
In the early test process, due to the low bearing capacity of the designed single pile, the equipment used for the test on site was relatively simple. With the development of test technology, the counterweights in the reaction platform have developed from soil mounds, pile drivers, water tanks, sand bags, etc. to concrete prefabricated blocks, steel ingots, or anti-anchors using engineering piles. The reaction force device has the diversified reaction force device of the anchor pile reaction force device, the pressure weight reaction force device, the combined reaction force device of piled heavy anchor piles, and the ground anchor reaction force device. In this way, on the one hand, the construction period is shortened, and on the other hand, the safety of the test is improved. The booster pump in the loading equipment has developed from a manual oil pump to an AC electric oil pump, a DC electric oil pump, and a fully automatic AC and DC electric oil pump. The measuring gauge used for observation has also developed from a mechanical dial gauge to a large-range, high-precision displacement sensor. On-site testing is replaced by a static load tester that automatically loading and unloading, records, and judges stability by manual meter reading by testers.
So, what devices will be used in the vertical compression test of single piles during the field test? And how to choose?
01 Reaction system
Common reaction devices are composed of steel beams of different specifications, buttresses, counterweights (concrete blocks or steel blocks), etc.
Single pile vertical compressive static load system often use anchor pile reaction devices, pressure weight reaction devices, anchor pile pressure combined reaction devices, and ground anchor reaction devices.
The steel beam used in the test includes the main beam and the secondary beam. The cross-sectional size of the steel beam must be determined by calculation and meet the three main requirements of strength, overall stability and rigidity. The first two guarantee the safety of the steel beam in use, and the latter guarantee that there will be no excessive deformation for normal use. If it is used in the ballast reaction device, the length of the steel beam needs to be considered to ensure that the reaction platform is within a safe height.
anchor pile pressure combined reaction devices
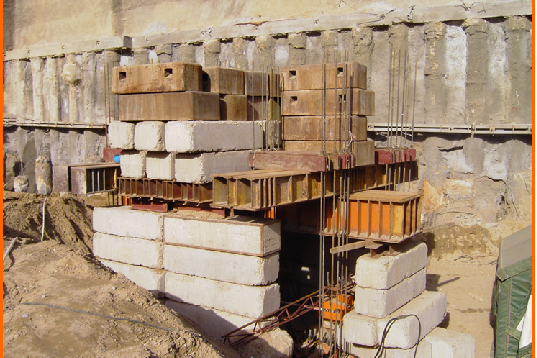
pressure weight reaction devices
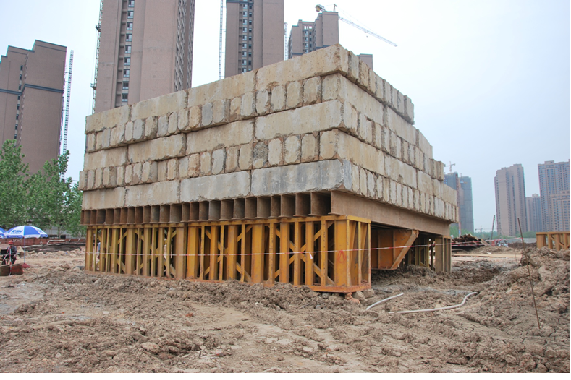
anchor pile reaction devices
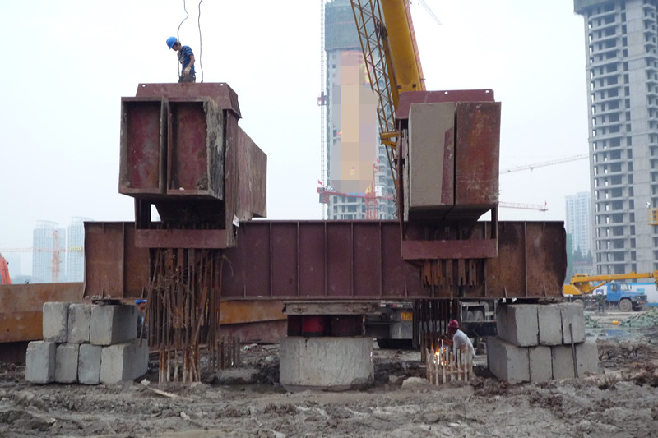
ground anchor reaction devices
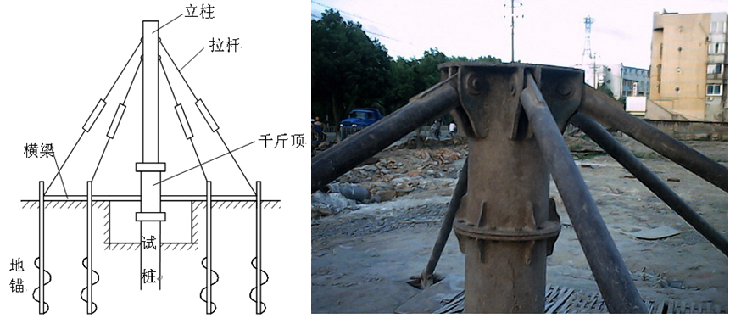
Regardless of the load reaction device, the reaction force provided by the loading reaction device shall not be less than 1.2 times the maximum loading value (some specifications have higher requirements, which shall be implemented according to the test specification), and the components of the loading reaction device shall meet the requirements of bearing capacity and deformation.When the anchor pile reaction device and the anchor pile pressure combined reaction device are used, when engineering piles are used as anchor piles, the number of anchor piles should not be less than 4, and the uplift of anchor piles should be monitored.The ballast should be fully added once before the test, and placed evenly and firmly on the platform, and the compressive stress exerted by the ballast on the foundation should not be greater than 1.5 times the characteristic value of the bearing capacity of the foundation. When conditions permit, engineering piles should be used as the fulcrum for surcharge.
02 Loading voltage stabilizing device
The loading and stabilizing device includes oil pumps, jacks, hydraulic oil pipes, diverter valves, unloading valves and other components.
Jack Selection
Static load tests generally use hydraulic jacks, and jacks of different tonnages can be selected according to different tonnage requirements.
At present, there are two types of jacks on the market, one is a single oil circuit jack, and the other is a double oil circuit jack; if the site needs instrument-controlled automatic unloading, a dual oil circuit jack should be selected.
When selecting a jack for the static load test, the pressure of the test pressure gauge, oil pump, and oil pipe at the maximum load should not exceed 80% of the specified working pressure (or 1.2 times the requirements of some specifications). And some areas clearly require that the measured value corresponding to the maximum test load of the jack should be controlled within the range of 25%-80% of the full range (or the range of the jack should not be greater than 3.0 times the maximum load). Specific requirements need to be checked with corresponding test specifications.
one-way jack
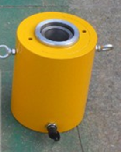
two-way jack
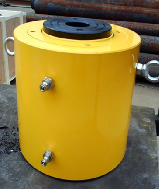
When two or more jacks are used for loading, their models and specifications should be consistent. All the jacks should work in parallel and synchronously, and the center of their resultant force should coincide with the centroid of the cross-section of the interposed pile. The purpose is to avoid the eccentricity of the tested pile. If the eccentricity is serious, the test data will be distorted, the reaction force will not be enough to test the real bearing capacity value, and the test pile and test equipment will be damaged if it is serious.
Note: In order to ensure consistent pressure in the test oil circuit, there should be no pressure maintaining device on the jack.
Oil pump selection
At present, there are many types of oil pumps on the market. When conducting engineering tests, the following points should be considered for selection:
1. The rated oil output of the oil pump is the oil output per minute when the oil pump is running. For example, in a large-tonnage test, it is not advisable to choose an oil pump with a rated oil output that is too small, which will cause the loading time to be too long. In the small tonnage test, it is not advisable to choose an oil pump with an excessively large rated oil output, otherwise the phenomenon of over-loading will often occur during the loading process.
2. Oil pump tank size. It is also an element of selecting an oil pump. For example, when carrying out a large tonnage test, choose an oil pump with a small fuel tank, and the oil pump needs to be refueled many times during the test. However, when unloading, the oil pump needs to be oiled, which increases the burden on the on-site inspectors. However, there is a problem that the large fuel tank oil pump is difficult to carry during the process of transportation, so it is necessary to choose reasonably.
3. The maximum loading capacity of the oil pump. The maximum loading capacity of the oil pump is also an important factor in the selection of the oil pump. For example, the maximum loading capacity of the oil pump can only be loaded to 40MPa, which will lead to the situation that it cannot be applied in the later stage of the test. Therefore, it is necessary to choose the maximum loading capacity of the oil pump reasonably.
Fully Automatic Oil Pump
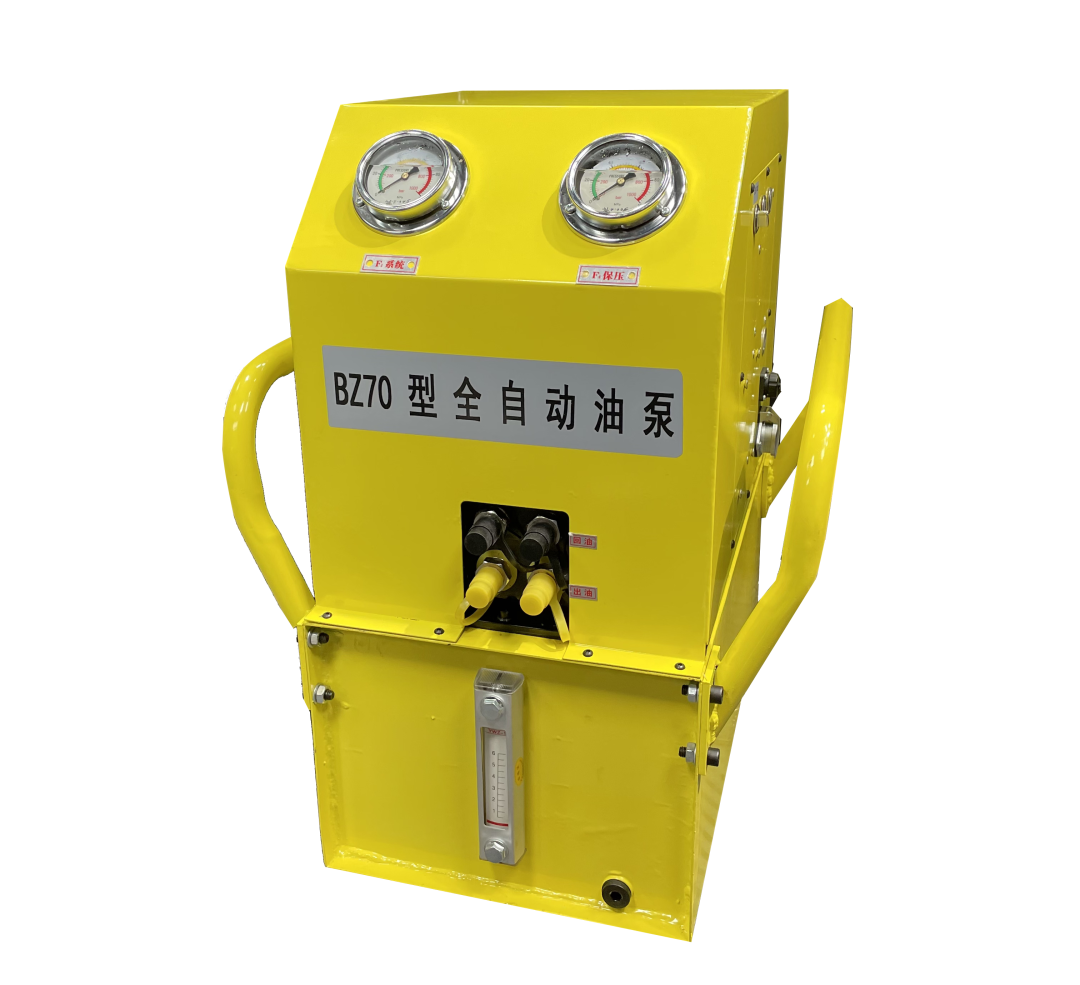
Electric Oil Pump
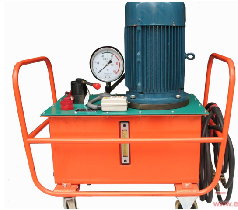
Manual Oil Pump
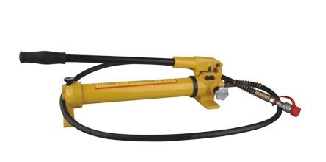
Load measuring device
The static load test controls the lifting of the jack by controlling the oil pump, so as to realize the application and unloading of the load. The load measurement generally adopts the following two forms: one is to measure directly with the load cell placed on the jack; the other is to measure the oil pressure through a pressure gauge or pressure sensor connected in parallel to the oil circuit of the jack, and convert the load according to the jack rate curve.
Measuring load with load cells is a direct measurement. In the single pile vertical compression test, the load cell is placed above the jack to directly measure the load value. When using a load cell test, the pressure measurement range and error only depend on the range and accuracy of the sensor, and have nothing to do with the size of the jack used. The load cell needs to be calibrated before the measurement.
Common load cell accuracy grades are 0.1, 0.25, 0.5, 1.0, etc., and the measuring ranges are 100kN, 200kN, 500kN, 1000kN, 2000kN, 3000kN, 5000kN, 8000kN, 10000kN, etc. When choosing to carry out the test, the appropriate load cell should be selected according to the test specification, maximum test load value and other information.
Load cell installation site
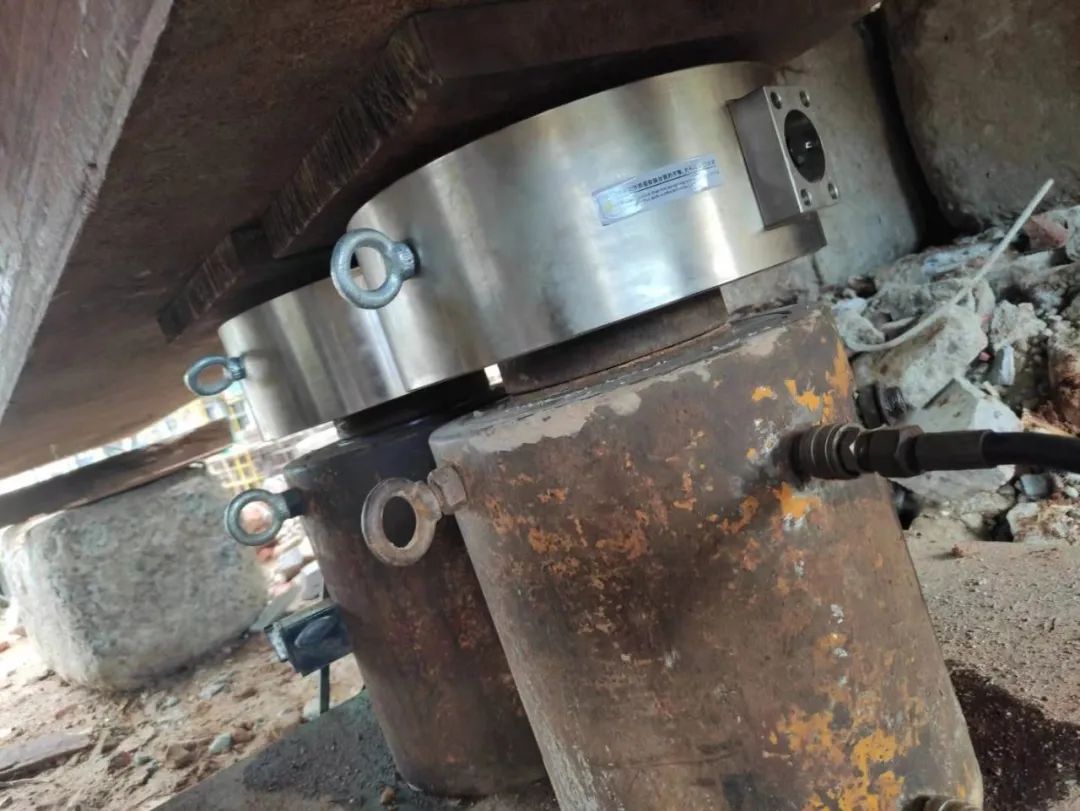
The load measured by the oil pressure gauge and pressure sensor is an indirect measurement. It directly measures the oil pressure of the jack, and the load of the jack is converted through the calibration curve of the jack. Relatively speaking, the pressure sensor with the same precision has higher precision and resolution than the oil pressure gauge.
The ranges of oil pressure gauges used for static load tests on the market mainly include 25MPa, 40MPa, 60MPa, 100MPa, etc., and the common accuracy grades are 0.1, 0.4, 1.0, 1.6, etc.
During the test, the pressure gauge and pressure sensor should be reasonably selected according to the test specification, the configuration of the jack and the maximum test load requirements.
pressure gauge
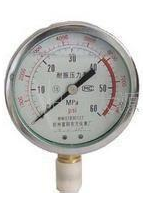
On-site installation diagram of pressure sensor
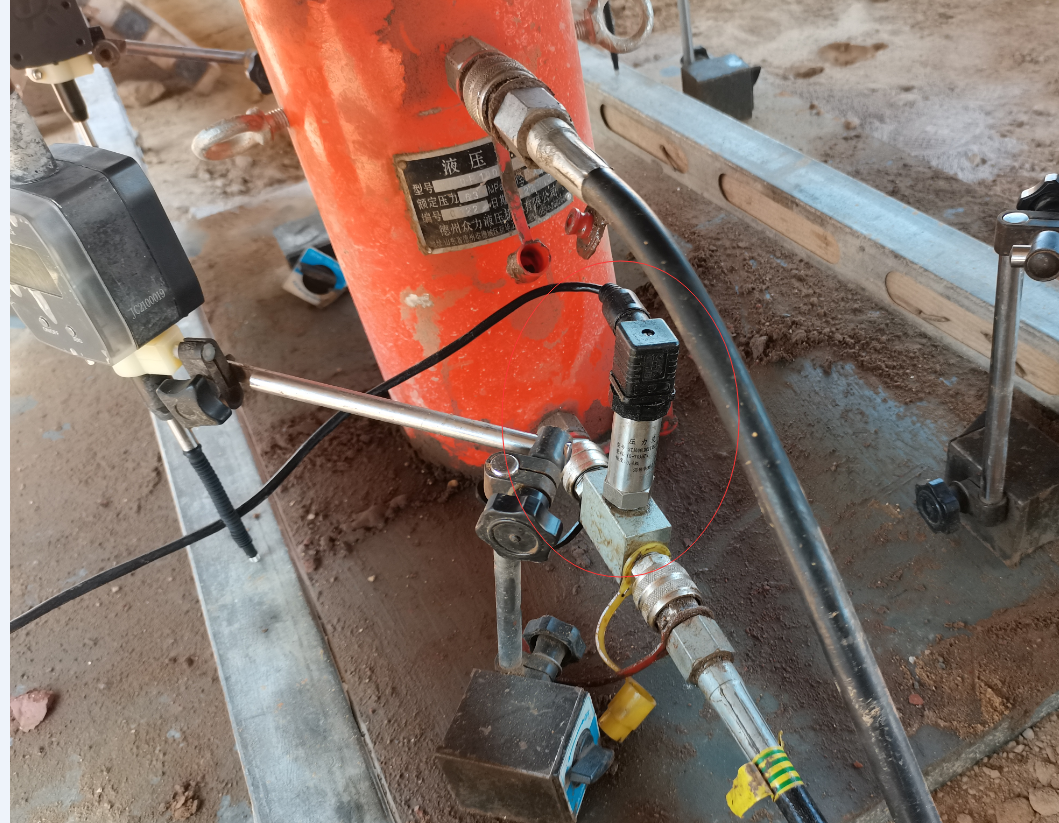
Displacement measuring device
The displacement measuring device is mainly composed of a reference pile, a reference beam and a dial indicator or a displacement sensor.
Displacement measuring device
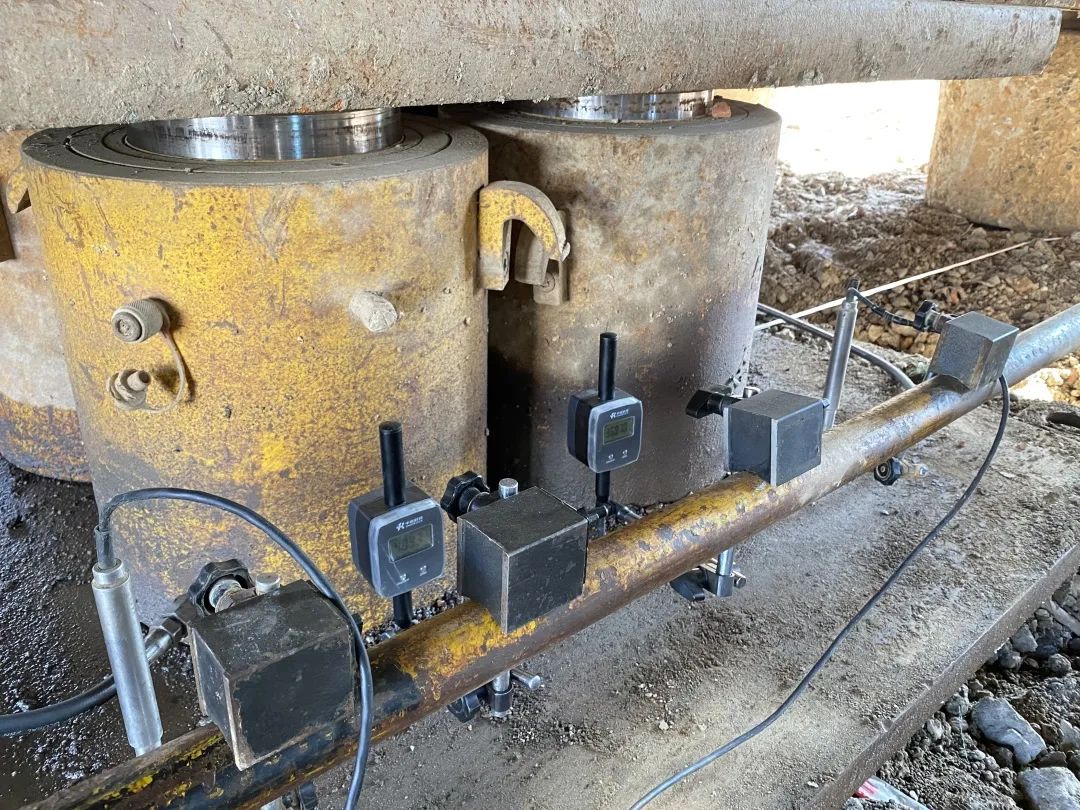
1. Datum beam and datum pile
Foundation piles and datum beams should in principle not move. However, due to the displacement of test piles and anchor piles, the influence of weather, sunshine, vibration and even tides caused by nearby construction and traffic, the reference piles or reference beams will have certain displacement or deformation. After the benchmark beam is firmly installed on the benchmark pile, the surrounding debris should be cleaned to ensure that the surrounding moving objects do not touch and affect the benchmark pile and benchmark beam during the test. The foundation piles should be driven to a sufficient depth below the ground, generally not less than 1m.
The benchmark beam should have sufficient rigidity, and I-beam should be used, and the height-span ratio should be less than 1/40. The disadvantage of steel is that the temperature expansion coefficient is large. In order to reduce the deflection deformation of the benchmark beam caused by temperature changes, one end is fixed on the benchmark pile, and the other end can move horizontally along the benchmark beam direction (simply supported on the benchmark pile).It is best not to set high-power lighting and heating equipment near the reference beam, and the reference beam can also be wrapped with heat insulating materials such as polystyrene to eliminate temperature effects.In addition, the reference beam should not be too long, because it is difficult to avoid the impact of climate and environment. The longer it is, the greater it will be affected by the external environment. In the actual test process, the reference beam can be covered with tarpaulin to prevent direct sunlight and wind and rain, and minimize the impact of the external environment on the test results.
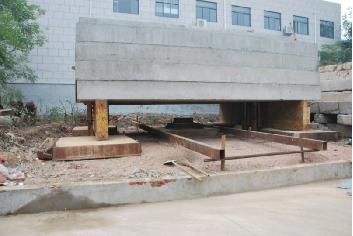
2. Dial gauge and displacement sensor
Displacement sensor or large range dial indicator should be used for settlement measurement of foundation piles. The commonly used dial gauge ranges are 50mm, 30mm and 10mm. The larger the range, the lower the qualification rate of periodic verification. However, the smaller the range of dial gauge used for settlement measurement will cause frequent adjustment and affect the measurement accuracy.
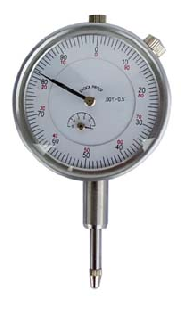
Dial gauge
The working principle of the displacement sensor is to convert the displacement signal into digital signal or signal for easy measurement and reading. The displacement sensor has a higher degree of automation than the dial indicator and can be used with a static load tester. At present, displacement sensors introduced by some manufacturers also have waterproof function, wireless connection and other functions, which are easier to operate and adapt to the site environment.
The dial indicator and displacement sensor shall be calibrated regularly during use, and the intermediate check shall be carried out frequently. The displacement sensor shall be equipped with clamp and gauge frame, which shall be connected with the reference beam. The clamp and gauge frame shall be free of deflection.
Capacitive displacement transducer
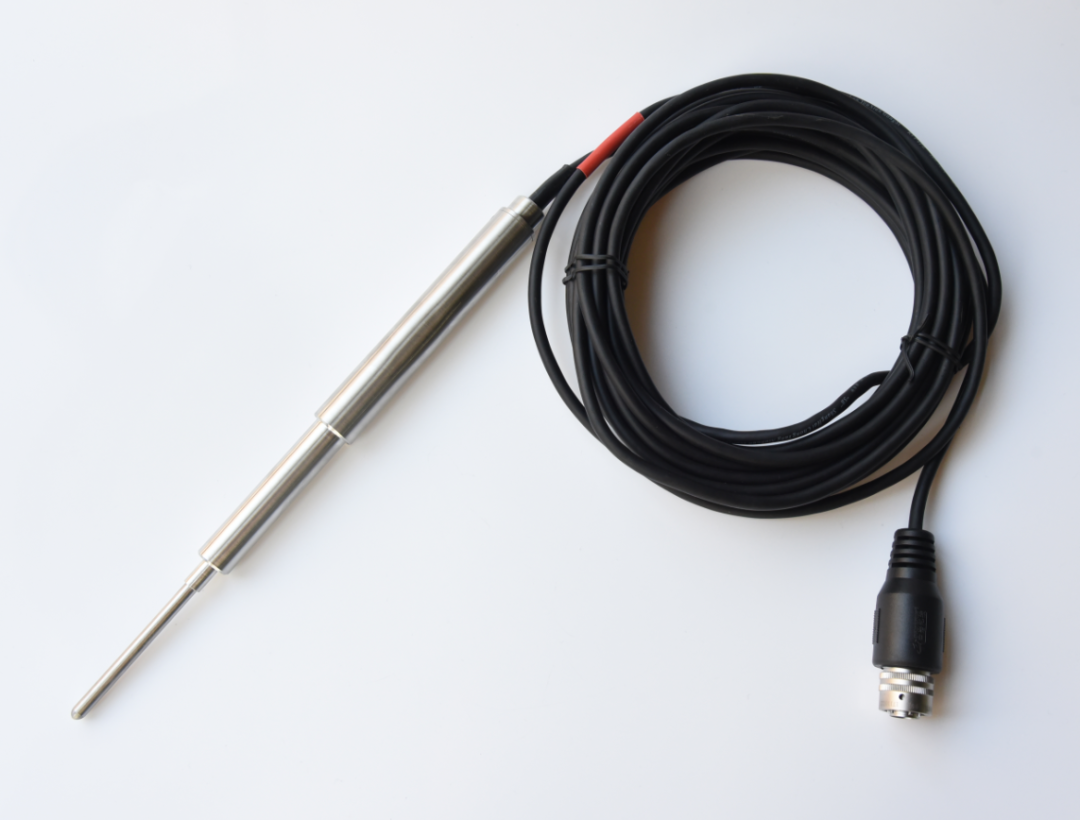
FM displacement sensor
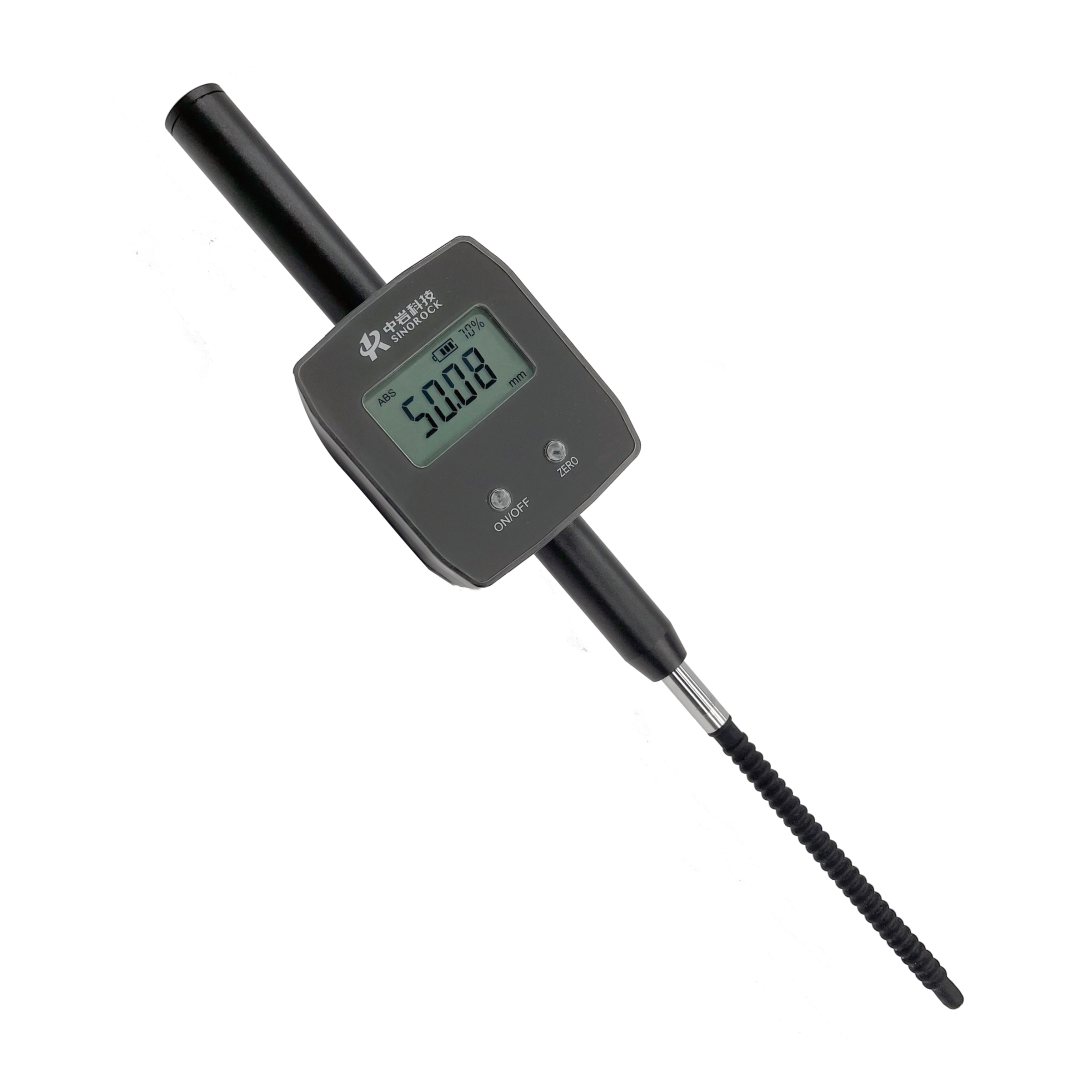
Wireless displacement sensor
In the vertical compressive static load test of a single pile, the settlement measurement plane should be below 200 mm from the pile top, and the distance from the measurement plane to the pile top should not be less than 0.5 times the pile diameter, whichever is greater. For piles with diameter or side width greater than 500mm, four dial indicators or displacement sensors shall be symmetrically arranged in two directions. For piles with diameter or side width less than 500mm, two dial indicators or displacement sensors can be symmetrically installed. The instruments shall be arranged symmetrically and at the same level.
The surface of the measuring point shall be treated to make it firmly fixed on the pile body. It is not allowed to set settlement observation points on the bearing plate or jack to avoid inaccurate settlement observation data caused by the deformation of the bearing plate.
Auto Data Collection device
After the 1990s, major manufacturers have developed automatic static load instruments, and more and more test units have begun to use automatic static load test equipment to replace traditional measurement methods. It has solved the problems that have puzzled the inspectors for a long time, changed the original static load test tools, greatly improved the working conditions, improved the test accuracy, standardized the static load test, and made a great step forward in the level of pile foundation testing.
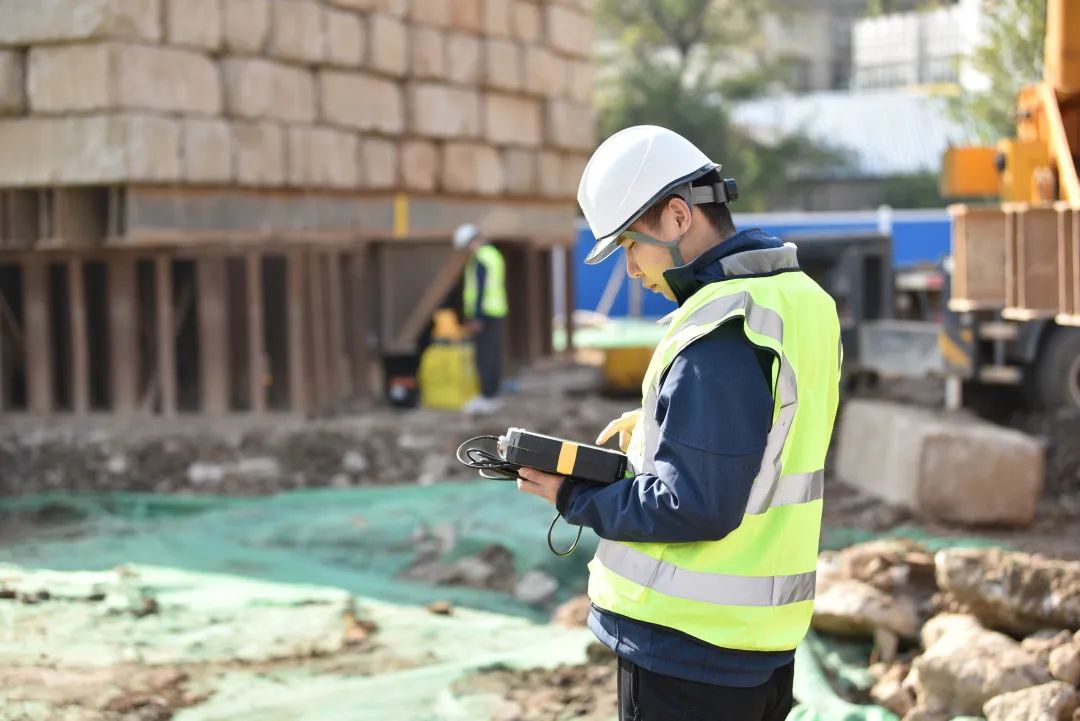
The static load test is the most accurate and direct method to detect the bearing capacity of pile foundation at present. In order to standardize the testing behavior, ensure the authenticity and reliability of the data, and put an end to fraud, local construction administrative departments or industry associations have successively implemented real-time monitoring and management of the static load test, standardize the testing behavior, control the testing quality, and strive to ensure the long-term healthy and orderly development of the testing market.