As the basic device for defect testing of cast-in-place concrete piles, the ultrasonic pile integrity tester can generate repetitive electric pulses and excite the transmitting transducer. The ultrasonic waves emitted by the transmitting transducer are coupled into the concrete, and after transmission in the concrete, they are received by the receiving transducer and converted into electrical signals. The electrical signals are sent to the ultrasonic pile integrity tester, which will draw and record the waveform.
Principle
After the foundation pile is used to make holes and before the concrete is poured, embed a number of sonic logging pipes in the pile as the channels for the acoustic wave transmitting and receiving transducers. Start the test several days after the pile body concrete is poured. Apply the ultrasonic pile integrity tester in the longitudinal direction along the pile at certain intervals to detect the parameters of the acoustic waves passing through each cross section of the pile body. Then, process, analyze and judge the test data, and determine the location, range and extent of the pile concrete defects, thereby inferring the pile concrete continuity, integrity and evenness, and assessing the pile integrity level.
Data acquisition
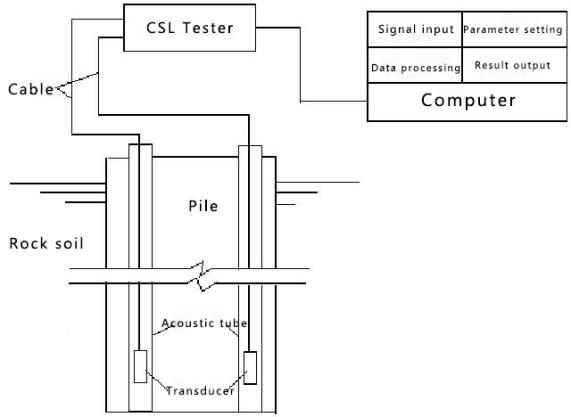
① Data acquisition: As a dedicated software, this program can realize all the indicators of cross-hole test supported by the hardware system of the auto-lift ultrasonic pile integrity tester. The user can select parameters or make a change according to the field test results.
② Waveform and wave train display: This program provides flexible, convenient and practical waveform and wave train display functions.
a. Waveform display area: for local observation of the waveform.
b. Real-time wave train display: the real-time wave train diagram of the waveform is displayed after adding self-judgment.
c. Absolute coordinate axis: gives the accurate time value corresponding to the data point.
③ The positions of measurement points are automatically determined.
④ Parameters can be read in real time:
a. The coordinates of the measurement point are determined by the automatic positioning system.
b. The sound interval, velocity and amplitude of the cross section can be frequently sent and received.
⑤ Parameters that can be adjusted in real time:
a. Gain: This program provides real-time adjustment of gain.
b. Delay: This program provides real-time adjustment of delay.
c. Self-judgment mode: Provide amplitude judgment, variance judgment and full-automatic judgment. Full-automatic judgment can accurately judge the first wave without inputting any parameters.
⑥ Data storage and reading: the data is stored or read in the wave train mode.
Wave train mode: A wave file is used to store the data of multiple measurement points of one pile.